佛山某汽车零部件厂张经理最近很头疼:IATF16949审核连续3次卡在 “过程审核”,客户审核员指着流程图问:“你们的PFMEA分析说冲压工序有模具磨损风险,现场为什么没看到对应的防错装置?” 原来,企业花大价钱编写的过程文件只是照搬模板,审核时只能拿 “文件齐全” 应付,实际生产中根本没按流程执行,最终导致客户订单暂缓。启航管理咨询团队通过 “精准定位 - 实战建模 - 动态优化” 三步法,帮这家企业让过程审核从 “走过场” 变成 “真管控”,3个月后顺利通过客户二方审核。
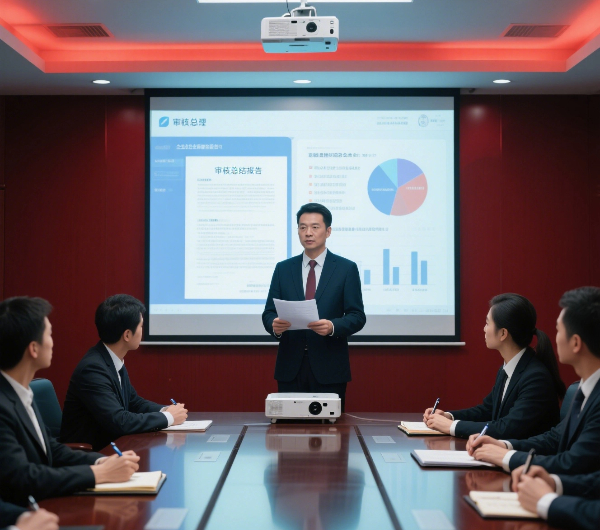
“两张皮” 根源:文件与现场脱节
- 用标准条款直接套流程,没结合企业实际工艺。例如:某注塑厂文件写 “首件检验需记录5项参数”,但现场设备自带自动检测功能,纸质记录成了重复劳动;
- 审核重点错位:过度关注记录表格是否填满,忽视 “过程是否真正降低风险”,比如工艺更改后未更新PFMEA,导致防错措施失效。
客户不认可的关键:缺 “证据链思维”
- 审核员要看 “过程有效性”,但企业只能提供 “文件存在”:▶ 问 “如何确保设备维护不影响生产”,回答 “有保养计划”,却拿不出保养后产能提升的数据对比;▶ 说 “优化了包装过程”,却没有客户投诉率下降的证据支撑。
第一步:精准识别核心过程 —— 用 “乌龟图” 画活流程
- 告别 “大而全” 的流程清单,用IATF16949的 “乌龟图” 工具聚焦关键过程:▶ 输入输出:明确每个过程的 “客户需求”(如客户订单)和 “交付成果”(如合格产品);▶ 资源匹配:标注完成过程所需的设备(如冲压机)、人员(如持证操作工)、方法(如控制计划);▶ 风险点标注:在乌龟图 “尾巴” 处列出3个核心风险(如 “模具老化→尺寸偏差”),对应防错措施(如 “增加首件全尺寸检测”)。
- 实战工具:启航提供《过程识别对照表》,帮企业快速判断 “哪些过程需要重点审核”(如直接影响产品质量的生产、检验过程)。
第二步:构建 “三维审核清单”—— 让审核项可量化、可追溯
- 从 “文件、现场、结果” 三个维度设计审核点:▶ 文件维度:检查控制计划是否覆盖乌龟图标注的风险点,作业指导书是否有图文并茂的操作步骤(如 “扭矩扳手校准后需贴绿色合格标签”);▶ 现场维度:突击检查员工是否按最新指导书操作,设备上的防错装置(如传感器)是否正常启用;▶ 结果维度:调取过程绩效数据(如某工序的CPK值、客户退货率),验证过程管控是否有效。
- 避坑要点:清单中60%以上的审核项需关联 “客户关注的质量指标”,例如客户在意的 “零公里缺陷率”,对应审核 “出货前全检流程” 的执行度。
第三步:建立动态改进机制 —— 让过程自己 “长” 出免疫力
班前会 “三问”
每天开工前花5分钟确认:“今天的关键过程风险是什么?”“对应的防错措施有没有落实?”“出现异常该找谁处理?”
异常闭环管理
用 “红黄绿三色看板” 追踪过程问题:▶ 红色:24小时内必须解决(如设备故障导致过程能力不足);▶ 黄色:3天内制定改进计划(如检验记录填写不规范);▶ 绿色:纳入下季度审核重点(如已解决的历史问题)。
- 工具升级:引入 “过程审核APP”,审核员现场扫码录入问题,系统自动关联责任部门,整改结果需上传照片证据,避免 “口头整改”。
一线员工参与
让班组长参与审核清单编制,把他们的实战经验(如 “夜班容易漏检”)转化为具体审核点;
客户标准前置
将客户二方审核的特殊要求(如某主机厂的 “分层审核表”)融入企业内部审核清单,避免重复准备。
IATF16949的过程审核卡关,本质是企业把 “体系” 当成了应付审核的文件游戏,而非服务生产的管理工具。从用乌龟图精准定位核心过程,到构建覆盖文件、现场、结果的三维清单,再到动态改进机制,关键是让审核项 “看得见、摸得着、有效果”。当审核员发现现场防错装置与PFMEA完全对应,过程绩效数据能证明质量提升,自然会认可体系的有效性。